MRP(Material Requirements Planning)は、製造業における資材所要量計画システムとして、生産計画に基づいて必要な資材の種類・数量・調達タイミングを計算する生産管理手法です。在庫最適化やコスト削減、生産効率向上を実現するMRPシステムについて、基本概念から導入メリット、ERPとの違い、実装時の注意点まで詳しく解説します。
目次
MRP(資材所要量計画)とは?基本概念と定義を解説
MRPの定義とMaterial Requirements Planningの意味
MRPとは、Material Requirements Planning(資材所要量計画)の略称で、製造業における生産に必要な資材の所要量を計算し、適切なタイミングで調達・製造を行うための生産管理手法です。MRPシステムは、生産計画をもとに必要な資材を必要な時に必要な量だけ確保することで、在庫を最小限に抑えながら効率的な生産を実現します。
MRP(Material Requirements Planning)は1960年代に開発された概念で、現在では多くの製造業で採用されている標準的な生産管理システムとなっています。MRPを導入することで、企業は資材の所要量を正確に把握し、在庫管理の最適化を図ることができます。
製造業における資材所要量計画の役割
製造業においてMRPは、生産管理の中核を担う重要な役割を果たしています。従来の生産管理手法では、経験や勘に基づいた在庫管理が行われることが多く、過剰在庫や欠品といった問題が頻繁に発生していました。
MRPシステムは、これらの課題を解決するために以下の機能を提供します。
- 生産計画に基づく正確な資材所要量の計算
- 在庫状況と発注タイミングの最適化
- 資材調達のリードタイムを考慮した計画立案
- 生産に必要な資材を適切なタイミングで確保
MRPを活用することで、製造業は生産性の向上と在庫コストの削減を同時に実現できます。特に、複雑な部品構成を持つ製品の製造において、MRPは欠かせない生産管理手法となっています。
MRPシステムが解決する生産管理の課題
MRPシステムは、従来の生産管理が抱えていた様々な課題を効率的に解決します。主な課題とMRPによる解決策は以下の通りです。
過剰在庫と在庫コストの問題に対して、MRPは生産計画を基に適切な所要量を計算し、必要最小限の在庫で生産を継続できるように最適化を行います。これにより、資材の在庫を大幅に削減し、キャッシュフローの改善にも貢献します。
また、欠品による生産停止のリスクについても、MRPシステムがリードタイムを考慮した発注計画を立てることで回避できます。システムが自動的に発注タイミングを計算し、生産に必要な資材を適切なタイミングで確保します。
生産計画の変更への対応も、MRPの重要な機能の一つです。市場の需要変動や顧客からの仕様変更要求に応じて、MRPシステムは瞬時に資材所要量を再計算し、新しい調達計画を提示します。
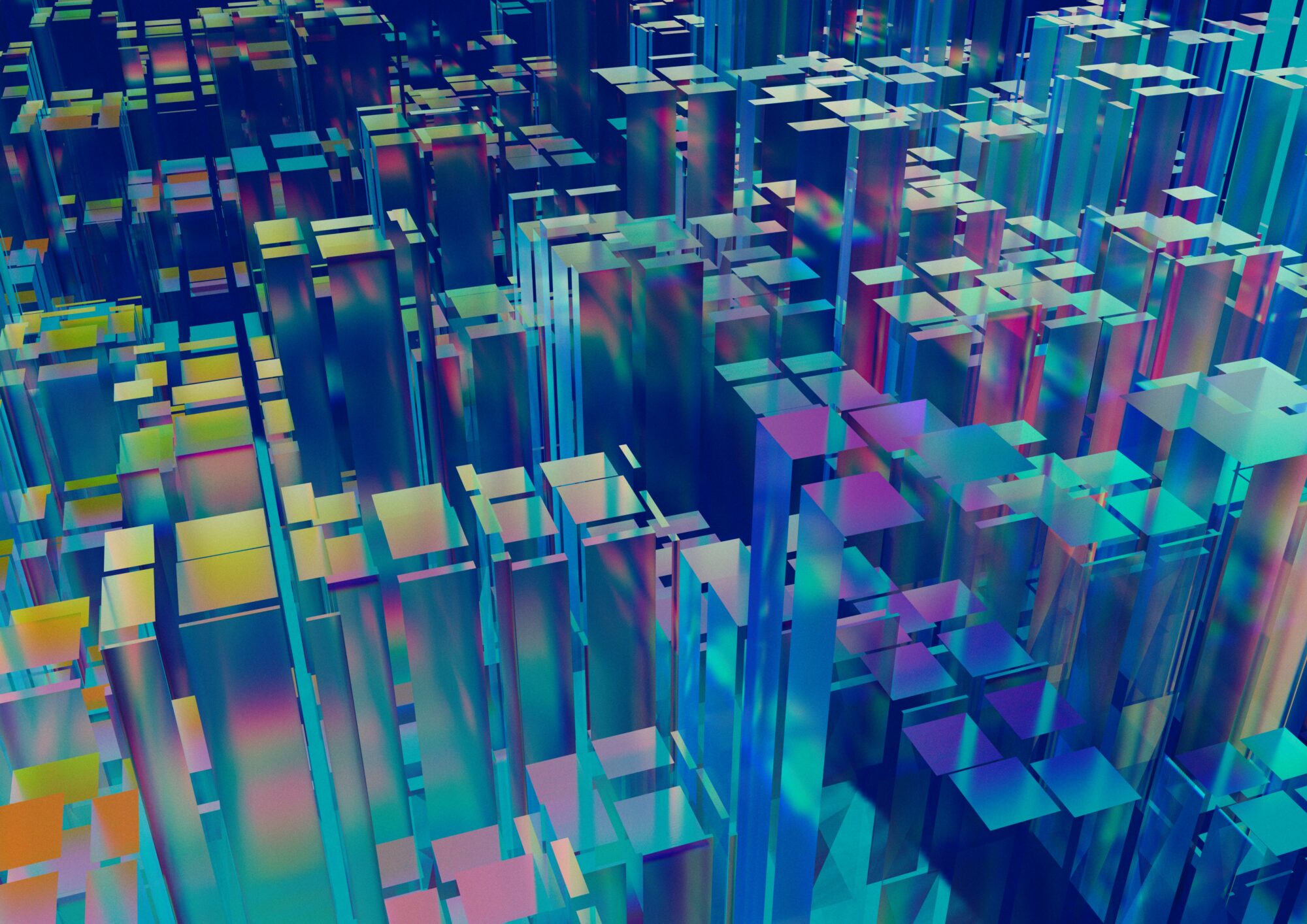
MRPの仕組みと資材所要量計算のプロセス
MRPシステムの基本的な計算ロジック
MRPシステムの計算ロジックは、生産計画から資材の所要量を段階的に展開していく構造になっています。システムは主生産計画(MPS:Master Production Schedule)を起点として、BOM(Bill of Materials:部品表)に基づいて各階層の部品や資材の必要量を計算します。
計算プロセスでは、まず完成品の生産数量が決定され、次にその完成品を構成する部品の所要量が算出されます。さらに、各部品を構成するより小さな部品や原材料の所要量を計算していきます。このような階層的な展開により、生産に必要なすべての資材の所要量を正確に把握できます。
生産計画から資材所要量を導出する流れ
MRPによる資材所要量の導出は、以下の段階的なプロセスで実行されます。最初に、販売予測や受注情報に基づいて主生産計画が策定されます。この計画には、どの製品をいつまでにどのくらい生産するかが明記されています。
次に、BOMを参照して各製品の構成部品とその使用量を確認します。MRPシステムは、製品の生産数量と部品の使用量を掛け合わせることで、各部品の総所要量を計算します。
現在の在庫量と既発注量を考慮して、実際に調達が必要な資材の量を算出します。さらに、各資材のリードタイムを逆算して、発注すべきタイミングを決定します。
BOM(部品表)とリードタイムの重要性
BOMは、MRPシステムの精度を左右する最も重要なマスタデータです。正確なBOMがなければ、適切な資材所要量の計算は不可能になります。BOMには、製品を構成するすべての部品とその使用量、組み立て順序などの情報が詳細に記録されています。
リードタイムは、資材の発注から納入までにかかる時間を表し、MRPの発注タイミング計算に不可欠な要素です。適切なリードタイム設定により、生産に必要な資材を過不足なく、最適なタイミングで確保することができます。
在庫情報と発注タイミングの最適化
MRPシステムは、リアルタイムの在庫情報を活用して発注タイミングを最適化します。システムは現在の在庫量、予定入庫量、予定出庫量を総合的に判断し、在庫が不足する前に適切な発注指示を出します。
また、安全在庫の概念も組み込まれており、需要変動や納期遅延などのリスクを考慮した在庫レベルを維持します。これにより、予期しない需要増加や供給遅延に対しても柔軟に対応できる体制を構築できます。
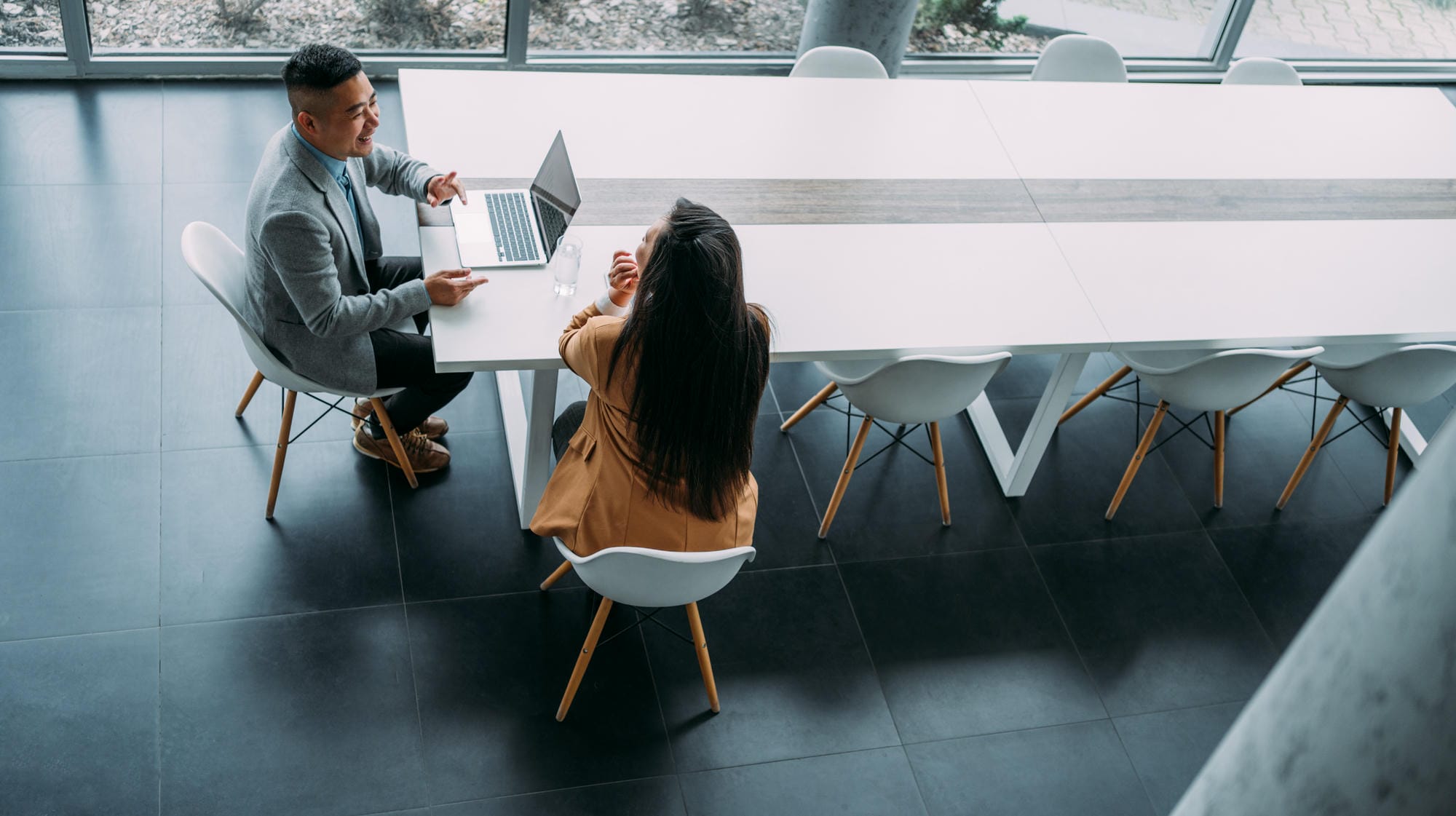
MRP導入による生産管理の効率化とメリット
在庫最適化によるコスト削減効果
MRPを導入することで得られる最大のメリットの一つが、在庫最適化によるコスト削減効果です。従来の生産管理では、需要予測の不正確さや安全在庫の過剰設定により、多額の在庫コストが発生していました。
MRPシステムは、生産計画に基づいて必要な資材を必要な時に必要な量だけ調達することで、在庫を最小限に抑え、在庫コストを大幅に削減します。一般的に、MRP導入により在庫コストは20-30%削減されると言われています。
また、在庫の回転率が向上することで、キャッシュフローの改善にも大きく貢献します。資材に投資された資金がより早期に回収され、企業の財務体質の強化につながります。
生産計画の精度向上と納期管理の改善
MRPの導入により、生産計画の精度が大幅に向上します。システムが正確な資材所要量を計算することで、生産に必要な資材を確実に確保でき、計画通りの生産が可能になります。
納期管理についても、MRPは顕著な改善効果をもたらします。資材の調達リードタイムを正確に把握し、生産スケジュールとの整合性を取ることで、納期遵守率の向上を実現します。多くの企業では、MRP導入により納期遵守率が90%以上に改善されています。
資材調達の効率化と調達コスト削減
MRPシステムは、資材調達の効率化においても大きな効果を発揮します。正確な所要量計算により、資材の過剰発注や緊急発注を大幅に削減できます。これにより、調達コストの最適化が実現されます。
また、計画的な発注により、サプライヤーとの長期契約や数量割引の交渉が可能になり、調達単価の削減にもつながります。さらに、発注業務の標準化により、調達部門の業務効率も向上します。
生産性向上と業務プロセスの標準化
MRP導入は、生産性の向上にも大きく貢献します。正確な生産計画と資材確保により、生産ラインの稼働率が向上し、無駄な待機時間が削減されます。
業務プロセスの標準化も重要なメリットです。MRPシステムの導入により、生産管理業務が標準化され、属人的な業務から脱却できます。これにより、業務品質の向上と人材育成の効率化が実現されます。
さらに、システムによる自動計算により、手作業による計算ミスが削減され、全体的な業務品質の向上につながります。多くの企業では、MRP導入により生産性が15-25%向上したという報告があります。
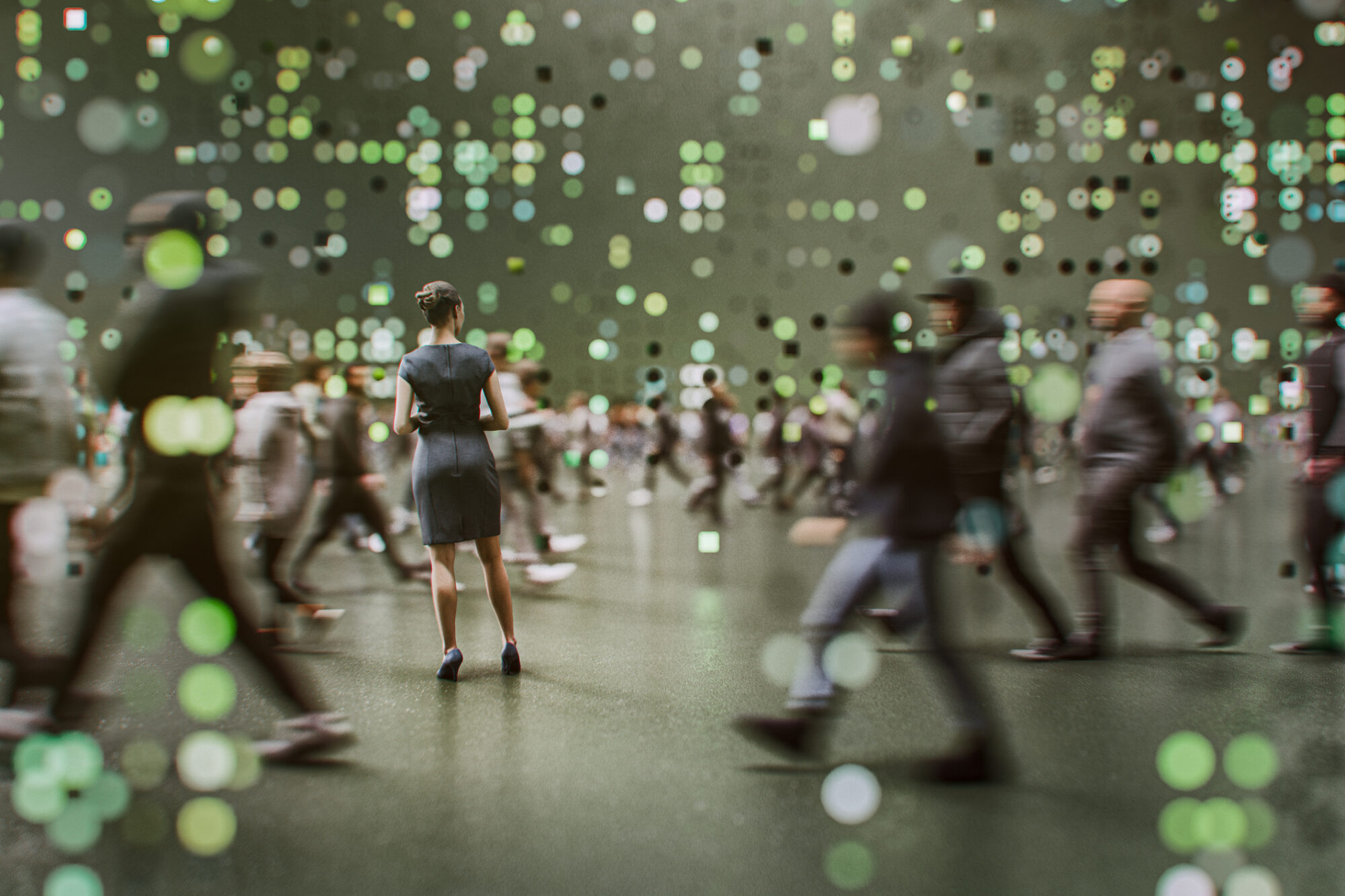
MRPとERP・MRP2・JITとの違いと使い分け
MRPとERPシステムの違いと連携関係
MRPシステムとERPシステムは、製造業における生産管理において重要な役割を果たしますが、その機能範囲と目的には明確な違いがあります。MRPは資材所要量計画に特化したシステムであり、生産に必要な資材の所要量を計算し、適切なタイミングで調達する仕組みです。一方、ERPは企業全体の業務プロセスを統合的に管理するシステムで、MRP機能も内包しています。
MRPシステムは、生産計画をもとに資材の所要量を計算し、在庫管理と連携して最適な発注タイミングを決定します。これにより、在庫を最小限に抑えながら、生産に必要な資材を確実に調達できます。一方、ERPシステムは販売管理、財務管理、人事管理なども統合し、企業全体の業務効率化を図ります。
MRPとERPの連携により、生産管理の効率化と全社的な業務最適化が同時に実現されます。小規模な製造業では単独のMRPシステムから始め、事業拡大に応じてERPシステムへの移行を検討することが一般的です。
MRP2(Manufacturing Resource Planning)との違い
MRP2は、従来のMRPシステムを拡張し、製造リソース全体を管理する概念です。MRPが資材所要量計画に重点を置くのに対し、MRP2は人的リソース、設備能力、生産能力も含めた包括的な生産管理手法となっています。
MRP2システムでは、資材所要量計画に加えて、作業負荷計画、能力所要量計画、工程管理などの機能が統合されています。これにより、生産計画の実現可能性をより精密に評価し、生産性の向上を図ることができます。
現在では、MRP2の概念はERPシステムに発展し、製造業における標準的な管理手法として定着しています。MRPからMRP2への発展は、製造業の生産管理が単なる資材管理から、総合的な製造リソース管理へと進化したことを示しています。
JIT(ジャストインタイム)生産方式との比較
JIT生産方式は、必要なときに必要な量だけを生産する手法で、MRPとは異なるアプローチを取ります。MRPは将来の需要予測に基づいて資材所要量を計算し、事前に資材を調達する「プッシュ型」の管理手法です。一方、JITは実際の需要に応じて生産を行う「プル型」の手法です。
MRPシステムは、生産計画に基づいて資材の所要量を計算し、在庫の最適化を図ります。JITでは、在庫を極限まで削減し、必要な資材を必要なときに調達することで、在庫コストの削減と生産効率の向上を目指します。
実際の製造現場では、MRPとJITを組み合わせた生産管理が行われることも多く、資材所要量計画の精度向上と在庫削減の両立が図られています。企業の生産特性や市場環境に応じて、適切な手法を選択することが重要です。
企業規模・業界特性に応じたシステム選択
MRPシステムの選択は、企業規模や業界特性に大きく左右されます。大規模製造業では、複雑な生産プロセスと多品種の資材管理が必要なため、包括的なERPシステムの導入が適しています。中小企業では、コストと機能のバランスを考慮し、MRPシステムから段階的に機能を拡張することが効果的です。
自動車産業や電子機器製造業など、部品点数が多く複雑な製品を扱う業界では、高度なMRP機能が求められます。これらの業界では、サプライチェーン全体の管理と、資材所要量計画の精密な計算が不可欠です。
一方、食品製造業や化学工業など、原材料の特性や有効期限を考慮する必要がある業界では、業界特化型のMRPシステムが適しています。適切なシステム選択により、生産管理の効率化と業務最適化を実現できます。
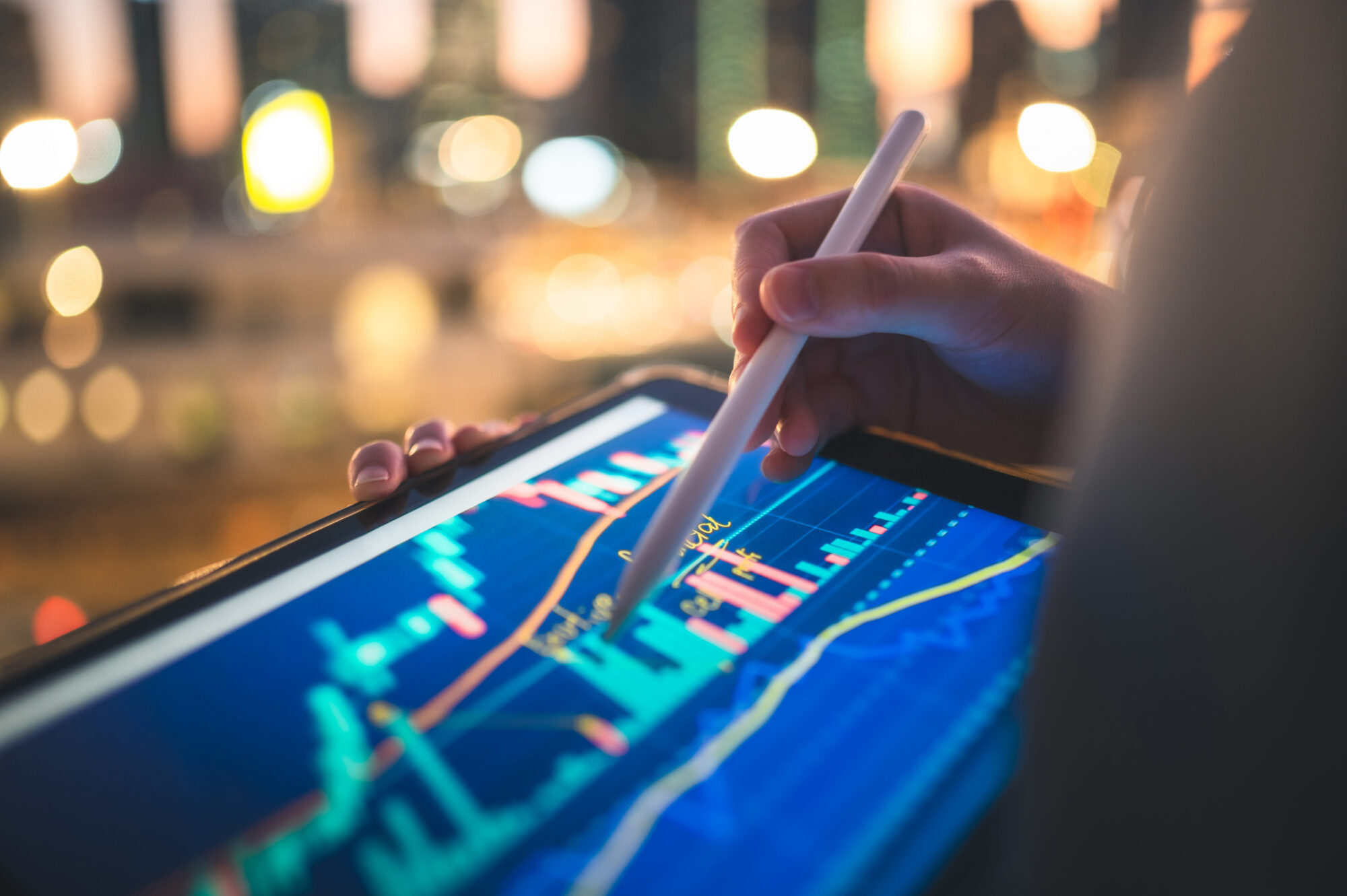
MRPシステムの種類と最新テクノロジー動向
従来型MRPシステムとクラウド型の特徴
従来型のMRPシステムは、企業内にサーバーを設置し、オンプレミス環境で運用される形態が主流でした。これらのシステムは、カスタマイズ性が高く、企業独自の生産管理プロセスに対応できる特徴があります。しかし、初期投資が大きく、保守・運用コストも継続的に発生します。
クラウド型MRPシステムは、インターネット経由でサービスを利用する形態で、初期投資を抑えながら高機能な資材所要量計画システムを導入できます。月額課金制により、企業規模に応じた柔軟な利用が可能で、システムの更新やセキュリティ対策も自動的に行われます。
クラウド型MRPシステムでは、リアルタイムでのデータ共有が可能で、複数拠点間での生産管理情報の同期が容易になります。これにより、グローバルな生産管理と、サプライチェーン全体の効率化が実現されます。
AI・機械学習を活用した予測MRP
AI技術の発展により、従来の固定的な計算ロジックに代わって、機械学習を活用した予測型MRPシステムが登場しています。これらのシステムは、過去の生産実績、市場動向、季節変動などの要因を分析し、より精密な資材所要量の予測を行います。
予測MRPでは、需要予測の精度向上により、在庫の最適化と生産計画の精度向上が同時に実現されます。機械学習アルゴリズムが継続的に学習することで、予測精度は時間とともに向上し、生産管理の効率化に大きく貢献します。
AI活用により、従来は人の経験に依存していた調達判断も自動化され、生産性の向上と人的リソースの有効活用が図られます。今後、AI技術の進歩とともに、より高度な予測機能を持つMRPシステムの普及が期待されます。
IoT連携によるリアルタイム生産管理
IoT技術とMRPシステムの連携により、製造現場のリアルタイム情報を活用した生産管理が可能になります。生産設備や在庫管理システムからのデータを自動収集し、MRPシステムに反映することで、常に最新の情報に基づいた資材所要量計算が実現されます。
IoT連携により、設備稼働状況、在庫レベル、生産進捗などの情報がリアルタイムで更新され、生産計画の動的な調整が可能になります。これにより、突発的な設備故障や需要変動にも迅速に対応できます。
センサーデータを活用した予知保全と組み合わせることで、設備停止による生産遅延を未然に防ぎ、安定した生産管理を実現できます。IoT技術の進歩により、製造業の生産管理はより精密で効率的なものへと発展しています。
DDMRP(需要駆動型MRP)の新しいアプローチ
DDMRP(Demand Driven Material Requirements Planning)は、従来のMRPの課題を解決する新しい手法として注目されています。従来のMRPが予測に基づく計画主導型であるのに対し、DDMRPは実際の需要に基づいて資材所要量を計算します。
DDMRPでは、戦略的在庫配置ポイントを設定し、これらのポイントでの在庫レベルを動的に管理します。これにより、需要変動に対する柔軟性を高めながら、在庫の最適化を図ることができます。
この手法では、サプライチェーン全体の可視化と、需要信号の迅速な伝達により、生産管理の効率化が実現されます。特に、需要変動の激しい市場において、DDMRPの効果は顕著に現れ、製造業の新たな生産管理手法として期待されています。
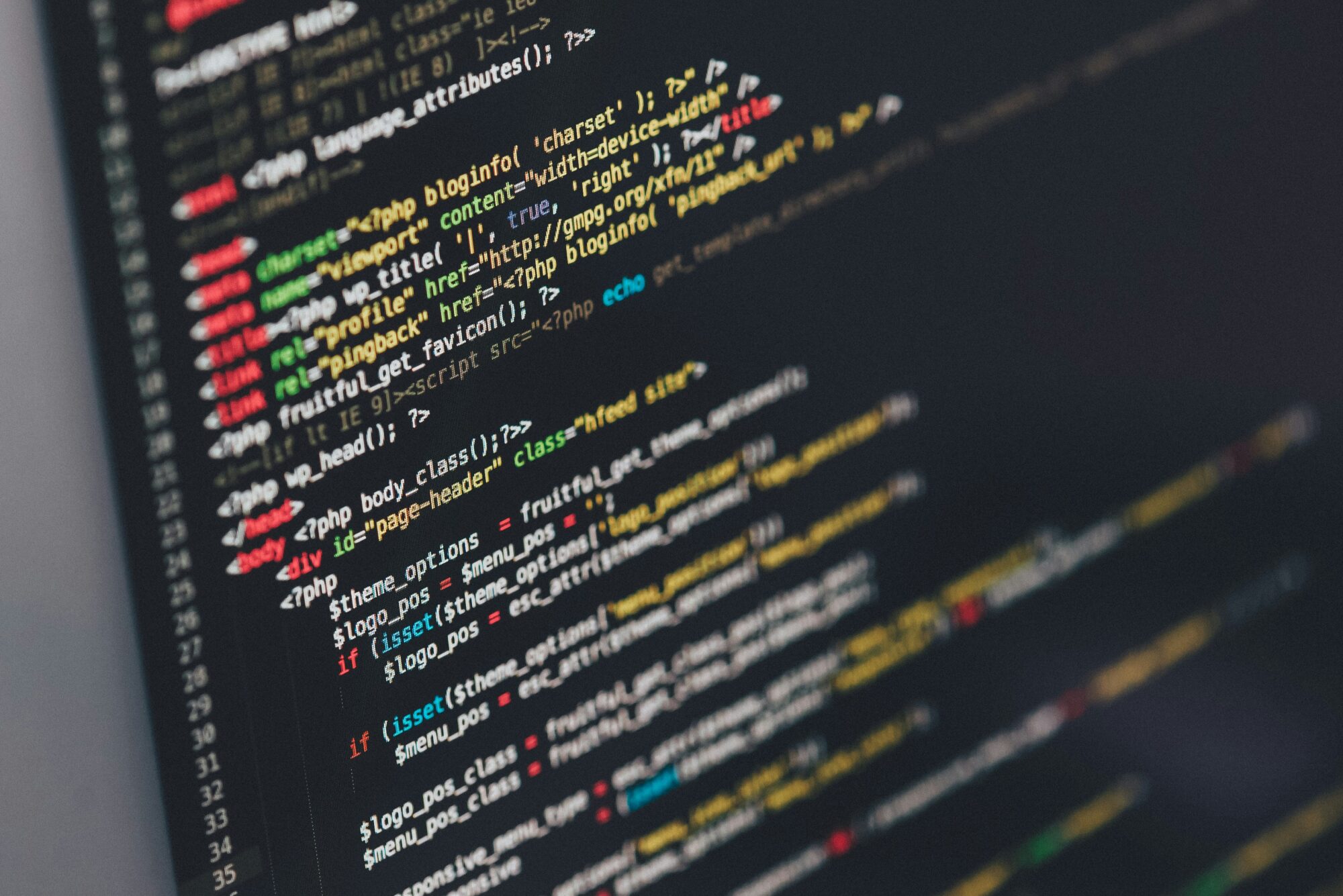
業界別・規模別MRP活用事例と成功パターン
自動車製造業でのMRP活用事例
自動車製造業では、数万点にも及ぶ部品を管理する必要があり、MRPシステムの導入効果が最も顕著に現れる業界の一つです。完成車メーカーでは、車種別・グレード別の生産計画に基づいて、各部品の所要量を精密に計算し、サプライヤーへの発注を最適化しています。
自動車業界特有のジャストインタイム生産との組み合わせにより、在庫を最小限に抑えながら生産ラインを止めることなく、必要な部品を調達する仕組みが構築されています。MRPシステムは、部品の調達リードタイムを考慮し、適切なタイミングでの発注を自動化しています。
また、モデルチェンジや仕様変更に対応するため、MRPシステムは柔軟な生産計画変更機能を持ち、設計変更情報を即座に資材所要量計算に反映させています。これにより、開発期間の短縮と生産効率の向上が同時に実現されています。
電子機器・精密機械業界での導入効果
電子機器製造業では、製品ライフサイクルが短く、多品種少量生産が特徴となっています。MRPシステムの導入により、頻繁な生産計画変更にも対応できる柔軟な資材管理が実現されています。
精密機械業界では、高価な材料や特殊部品を扱うため、MRPによる在庫最適化の効果が特に大きく、調達コストの削減と資金効率の改善が図られています。また、技術革新のスピードが速いため、部品の陳腐化リスクを最小限に抑える在庫管理が重要になります。
これらの業界では、MRPシステムと製品設計システムの連携により、設計変更が即座に生産計画に反映され、開発から量産までのリードタイム短縮が実現されています。品質管理システムとの統合により、不良品発生時の迅速な対応も可能になっています。
中小製造業におけるMRP導入のポイント
中小製造業では、限られた人的リソースと予算の中でMRPシステムを効果的に活用する必要があります。まず、現状の生産管理プロセスを整理し、MRPシステムで最も効果が期待できる領域を特定することが重要です。
中小企業では、シンプルで使いやすいMRPシステムの選択が成功の鍵となります。複雑な機能よりも、基本的な資材所要量計算と在庫管理機能を確実に運用できるシステムを選ぶことで、導入効果を最大化できます。
段階的な導入アプローチにより、まず主要製品や重要部品からMRPシステムを適用し、運用が安定した後に対象範囲を拡大していくことが効果的です。また、従業員の教育と変革管理に十分な時間をかけることで、システム定着率を高めることができます。
グローバル企業のサプライチェーン管理での活用
グローバル企業では、世界各地の生産拠点と調達先を統合的に管理するため、高度なMRPシステムが必要となります。時差や通貨変動、貿易規制などの要因を考慮した複雑な資材所要量計算が求められます。
グローバルMRPシステムでは、各拠点の生産計画を統合し、最適な調達戦略を策定します。地域間での資材融通や、為替リスクを考慮した調達先選択により、総合的なコスト最適化が実現されます。
また、各国の法規制や品質基準への対応も重要な要素となり、MRPシステムはこれらの要件を満たす資材調達を自動的に計画します。災害やパンデミックなどのリスクに対応するため、複数の調達ルートを考慮した柔軟な計画立案機能も不可欠です。
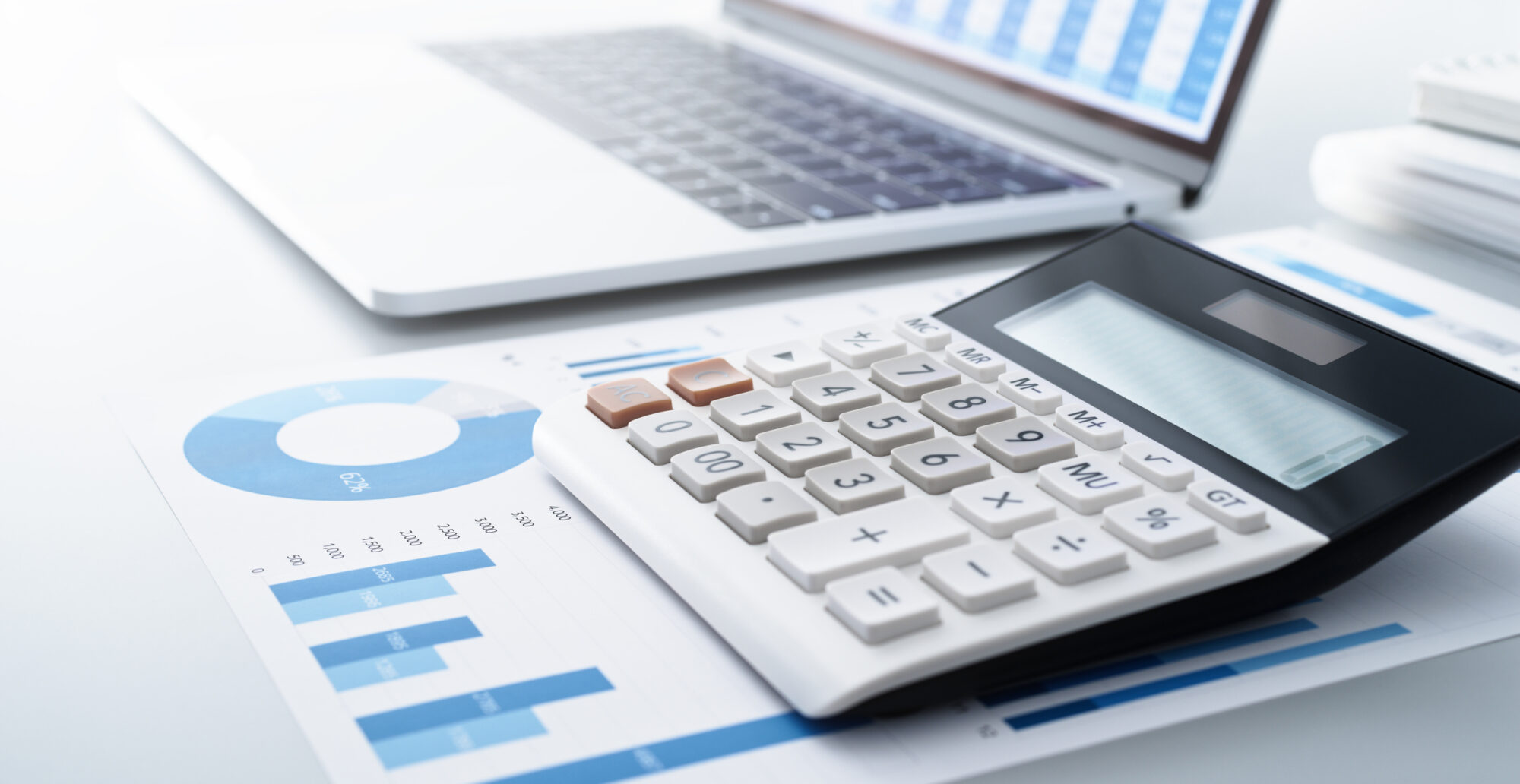
MRPシステム導入の進め方と実装プロセス
導入前の現状分析と課題の洗い出し
MRPシステム導入の成功には、導入前の現状分析が不可欠です。現在の生産管理プロセス、在庫管理手法、資材調達の流れを詳細に分析し、業務の無駄やボトルネックを特定します。生産計画の精度、在庫回転率、調達リードタイムなどの指標を定量的に評価することが重要です。
既存システムとの連携要件や、データ移行の範囲も事前に明確化する必要があります。部品表(BOM)の整備状況、在庫データの精度、生産実績の記録方法などを評価し、MRPシステムに必要なマスタデータの準備状況を確認します。
組織の準備状況も重要な要素で、MRP導入に対する経営層のコミットメント、現場の理解度、変革に対する意識などを評価します。これらの分析結果をもとに、MRPシステムに求める機能要件と、導入後の目標を具体的に設定します。
システム選定の評価基準と比較ポイント
MRPシステムの選定では、機能要件、技術要件、コスト要件を総合的に評価します。資材所要量計算の精度、在庫管理機能、生産計画との連携性、既存システムとの統合性などが主要な評価項目となります。
導入コストだけでなく、運用コスト、保守費用、教育コストも含めた総所有コスト(TCO)での比較が重要です。また、ベンダーのサポート体制、システムの拡張性、将来的な機能追加の可能性も評価基準に含めます。
業界特有の要件への対応度も重要な選定基準で、製造業の特性に応じたカスタマイズの容易さ、業界標準への準拠度なども評価します。実際の運用を想定したデモンストレーションや、類似企業での導入事例の確認により、システムの適合性を検証します。
段階的導入アプローチと運用開始までの流れ
MRPシステムの導入は、リスクを最小化するため段階的なアプローチが推奨されます。まず、パイロット製品や特定の製品群を対象として小規模な導入を行い、システムの動作確認と業務プロセスの検証を実施します。
第一段階では、基本的な資材所要量計算機能を中心に導入し、システムの安定性と計算精度を確認します。第二段階では、在庫管理機能との連携を強化し、発注自動化機能を追加します。最終段階では、生産計画システムとの完全統合を実現します。
各段階において、ユーザーテストと運用評価を十分に実施し、問題点の早期発見と改善を図ります。運用開始前には、全ユーザーを対象とした実践的な教育プログラムを実施し、システムの定着を促進します。
社内体制構築と従業員教育の重要性
MRPシステムの成功には、適切な社内体制の構築が不可欠です。プロジェクトチームには、IT部門、生産管理部門、調達部門、品質管理部門の代表者を含め、部門横断的な協力体制を構築します。プロジェクトマネージャーは、各部門の利害を調整し、全体最適の視点でシステム導入を推進します。
従業員教育では、MRPの基本概念から始まり、システムの具体的な操作方法、業務プロセスの変更点について段階的に教育を行います。特に、現場の作業者には、データ入力の重要性と、正確な実績報告の必要性を理解してもらうことが重要です。
教育プログラムは、座学だけでなく、実際のシステムを使用した実習を中心に構成し、実践的なスキルの習得を図ります。また、システム導入後も継続的な教育とフォローアップを実施し、ユーザーのスキル向上とシステムの効果的な活用を促進します。
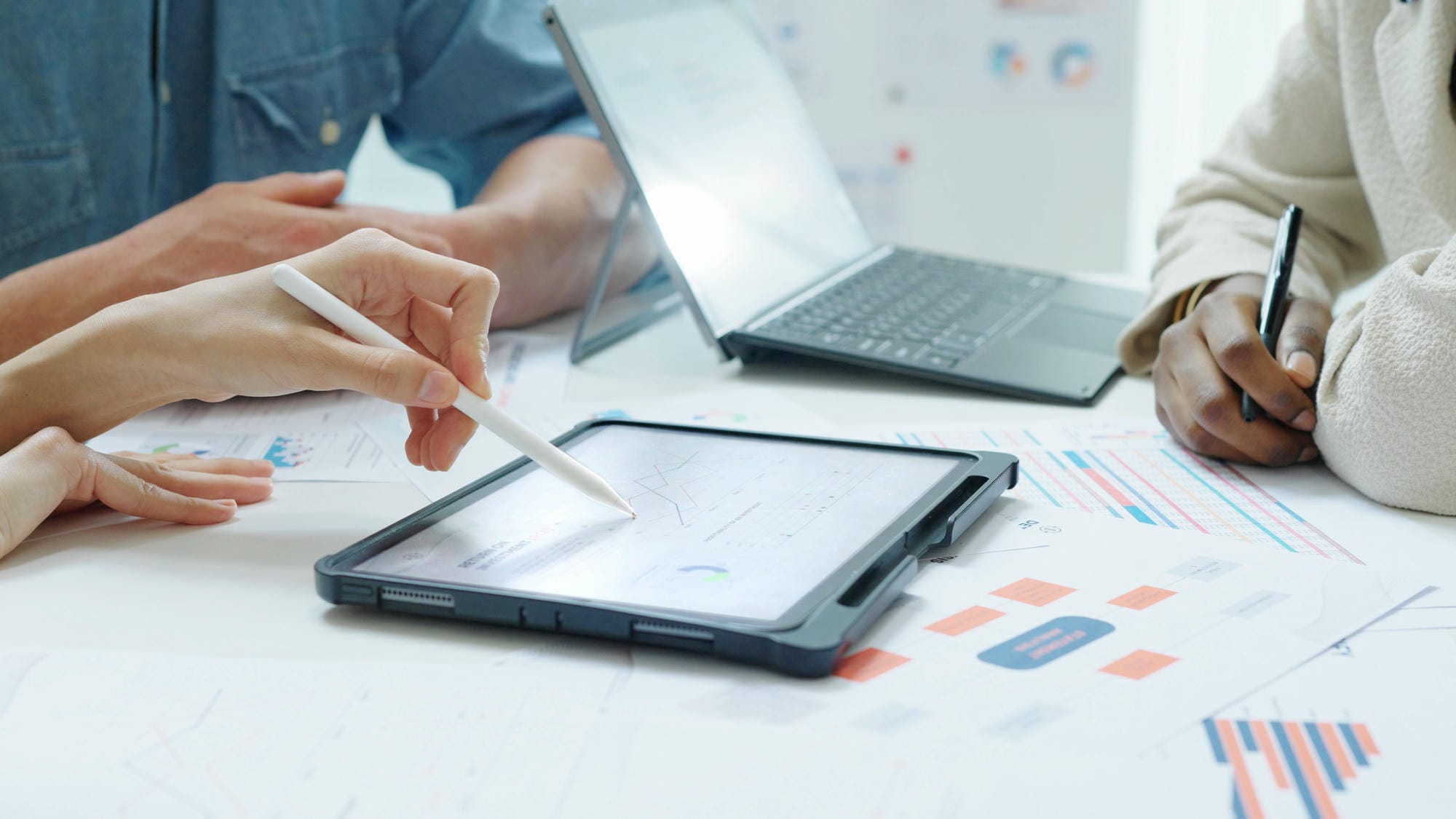
MRP導入時の注意点と失敗を避けるポイント
BOM整備とマスタデータ精度の確保
MRPシステムを導入する際に最も重要なのは、BOM(部品表)の精度とマスタデータの品質確保です。MRPは生産計画に基づいて資材所要量計画を自動計算するため、入力されるデータの正確性が結果の信頼性を直接左右します。
部品表の不整合や在庫情報の誤りがあると、MRPシステムは適切な所要量を計算できません。必要な資材の発注量が過大になったり、逆に不足が生じたりする可能性があります。導入前には、既存の部品表データを徹底的に整備し、在庫管理システムとの連携を確実に行う必要があります。
また、リードタイム情報や安全在庫の設定値についても、実際の生産現場の状況に合わせて適切に設定することが重要です。MRPを導入する企業では、データ整備に十分な時間と労力を投入することで、システムの効果を最大化できます。
部門間の情報共有体制とコミュニケーション強化
MRPシステムの成功には、営業、生産、調達、在庫管理などの各部門間での情報共有体制の構築が不可欠です。生産計画の変更や緊急オーダーの対応時には、リアルタイムでの情報共有が求められます。
特に、営業部門からの受注情報や生産部門からの製造進捗情報が遅れると、MRPシステムが算出する資材所要量計画の精度が低下します。部門間のコミュニケーション不足は、在庫の過不足や納期遅延の原因となるため、導入前に明確な情報共有ルールを策定する必要があります。
導入コストと効果測定・ROI算出方法
MRPシステムの導入には、ソフトウェアライセンス費用、システム構築費用、従業員研修費用などの初期投資が必要です。中小企業では数百万円から、大企業では数千万円規模の投資となることが一般的です。
MRPシステム導入の効果測定では、在庫削減効果、調達コスト削減、生産性向上による売上増加を定量的に評価することが重要です。投資対効果を適切に算出するためには、導入前の基準値を正確に把握し、導入後の改善効果を継続的に測定する体制を整備する必要があります。
運用定着までの課題と対策
MRPシステムは導入後の運用定着が最も重要な段階です。従業員がシステムを正しく活用できるまでには時間がかかるため、継続的な教育とサポート体制の構築が必要です。
また、システム導入初期には予期しない問題が発生することがあります。生産現場での混乱を最小限に抑えるため、段階的な導入アプローチを採用し、問題発生時の迅速な対応体制を整備することが重要です。MRPを導入する企業では、運用開始から安定稼働まで少なくとも6ヶ月から1年程度の期間を見込んでおくことが推奨されます。
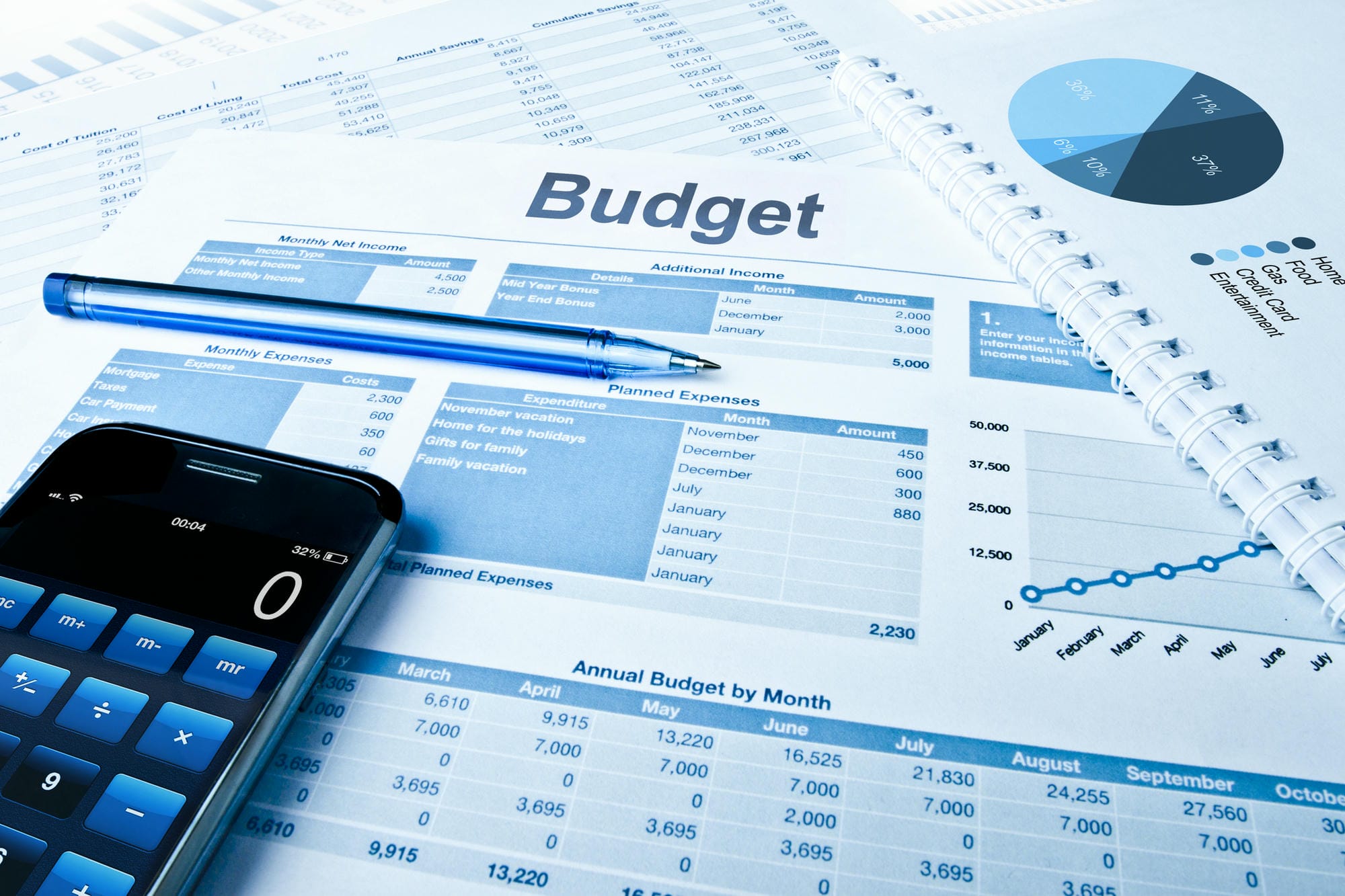
MRPの効果測定とKPI設定による継続改善
在庫回転率と在庫削減効果の測定
MRPシステムの導入効果を測定する主要な指標として、在庫回転率の改善があります。適切な所要量計算により、過剰在庫を削減しながら欠品リスクを最小化できます。
在庫削減効果の測定では、原材料、仕掛品、完成品それぞれの在庫レベルを月次で追跡し、導入前との比較を行います。一般的にMRPシステムの効果により、在庫水準を10~30%削減できることが期待されます。
生産計画精度と納期遵守率の向上度合い
MRPシステムは生産計画の精度向上にも大きく貢献します。資材の所要量を正確に計算することで、生産遅延や納期遅れを防ぐことができます。
納期遵守率の測定では、顧客への約束納期に対する実際の納期達成率を追跡します。MRPを導入した企業では、納期遵守率が85%から95%以上に改善する事例が多く報告されています。
調達リードタイム短縮と調達コスト削減効果
MRPシステムにより計画的な資材調達が可能になることで、調達リードタイムの短縮と調達コストの削減効果が期待できます。必要な資材を必要な時に適切な量だけ発注することで、緊急調達や大量発注による無駄を削減できます。
調達コスト削減効果の測定では、単価改善、発注回数最適化、在庫保管コスト削減などを総合的に評価します。
継続的なシステム最適化と改善サイクル
MRPシステムの効果を継続的に向上させるためには、定期的な見直しと改善サイクルの構築が不可欠です。市場環境の変化や生産条件の変更に応じて、パラメータの調整やシステムの機能拡張を行う必要があります。
月次または四半期ごとにKPIの見直しを行い、目標値に対する実績の分析を通じて、さらなる改善機会を特定することが重要です。継続的な改善により、MRPシステムの効果を最大化し、企業の競争力向上に貢献できます。
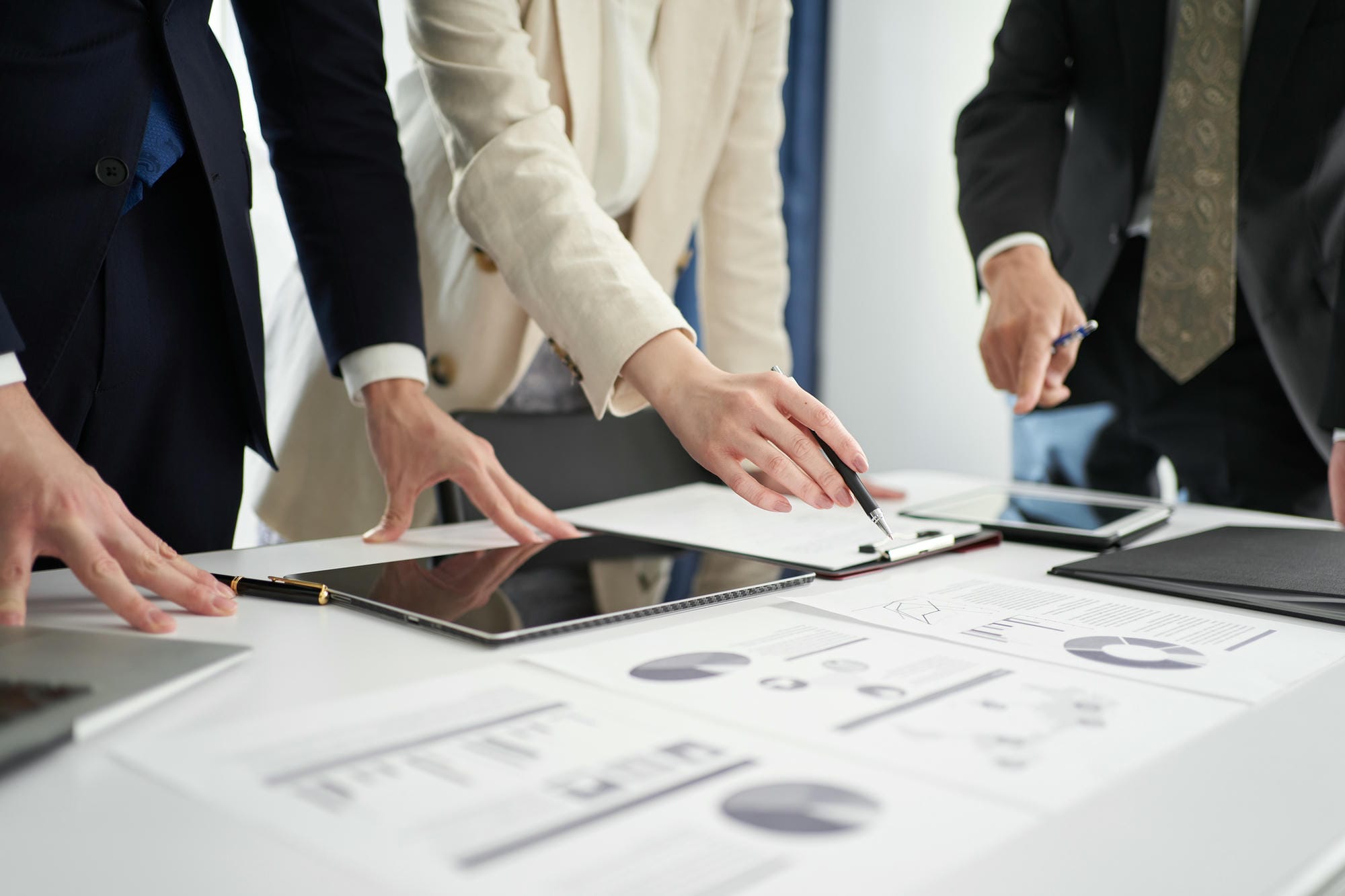
MRPとは|よくある質問(FAQ)
MRPシステムの導入期間と費用はどのくらい?
MRPシステムの導入期間は企業規模や業務の複雑さによって異なりますが、一般的に6ヶ月から18ヶ月程度を要します。中小企業では比較的短期間での導入が可能ですが、大企業では部門間の調整や既存システムとの連携に時間がかかることがあります。
導入費用については、パッケージソフトの場合は数百万円から数千万円、大規模なカスタマイズが必要な場合は1億円を超えることもあります。コンサルティングファームを活用する場合は、年間1000万円から1億円程度の費用が追加で必要になります。
小規模製造業でもMRP導入のメリットはある?
小規模製造業においても、MRPシステム導入によるメリットは十分に期待できます。特に部品数が多い製品を扱う企業や、受注生産を行う企業では、在庫管理の効率化や生産計画の精度向上による効果が顕著に現れます。
近年では中小企業向けのクラウド型MRPシステムも充実しており、初期投資を抑えながら段階的にシステムを導入することが可能です。従業員数が少ない企業でも、適切なシステム選択により生産性向上を実現できます。
既存の生産管理システムからの移行は可能?
既存の生産管理システムからMRPシステムへの移行は可能ですが、データの整合性確保と業務プロセスの見直しが重要です。特に、部品表データや在庫情報、取引先マスタなどの基幹データの移行には細心の注意が必要です。
移行時には、新旧システムの並行稼働期間を設けることで、データの整合性を確認しながら安全に移行を進めることができます。また、従業員への教育研修も重要な要素となります。
MRPとERPどちらを導入すべき?
MRPとERPの選択は、企業の規模や管理範囲によって決まります。製造業で生産管理に特化した機能が必要な場合はMRPシステムが適しており、会計や人事、販売管理なども含めた統合管理が必要な場合はERPシステムが適しています。
中小企業では段階的にMRPから始めて、必要に応じてERPへ拡張するアプローチも有効です。システム選択時には、現在の課題と将来の事業拡張計画を総合的に検討することが重要です。
MRP導入で失敗しないための最重要ポイントは?
MRP導入で失敗しないための最重要ポイントは、経営陣のコミットメントと現場の巻き込みです。システム導入は単なるツールの変更ではなく、業務プロセス全体の変革を伴うため、全社的な取り組みが必要です。
また、データの品質確保、段階的な導入アプローチ、継続的な教育研修の実施も成功の鍵となります。導入前の現状分析を十分に行い、明確な目標設定と効果測定の仕組みを構築することで、MRPシステムの効果を最大化できます。